
The Story of Triaxial Fabrics
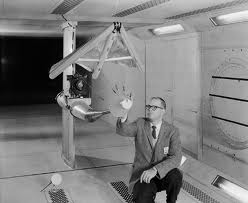
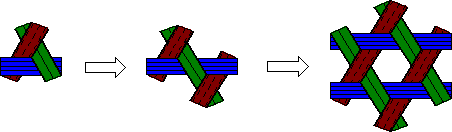
The first drawing shows one strand, for instance the horizontal one, being constrained from moving upward by the intersection of the other two strands. Expanding this intersection to two, the second illustration shows the horizontal strand is constrained from moving vertically in either direction. Finally extending the locked intersection configuration to a full unit shows all the strands are constrained from moving in any direction. The locked intersection characteristics and how they affect the performance of triaxial fabric is determined by the size of the yarns and the pitch distance between them. By modifying either of these variables, an amount of extensibility can be designed into the woven fabric, giving a truly engineered fabric structure.
Since this was such an “obvious” solution, Mr. Dow thought one could just go to the local fabric store, buy some “triaxial” fabric, build a parawing and re-run the wind tunnel tests. It took several years of patent research to determine no one, in the thousands of years of weaving fabric, had previously thought of this as a solution to the bias weakness problem in fabrics. Mr. Dow patented the concept in the U.S. and 16 other textile producing countries and in 1965 founded N.F. Doweave, Inc. to commercialize the product. By 1974, 17 Barber-Colman built production machines were operating in a pilot mill in King of Prussia, PA, each producing approximately 500 yards of triaxial material a week. Unfortunately, the textile industry has a high entrance threshold and by 1978 N.F. Doweave had exhausted its funding and had to close.
Barber-Colman acquired the assets of N.F. Doweave and after upgrading the design in certain areas produced 6 additional Triaxial Weaving Machines (TWM). Two of these machines were sold to a Jananese company, one to a British company and three to a domestic company. The three domestic machines were then purchased by an advanced textile and materials processing company and modified one of the machines to create a single end creel system. In the spring of 2010, Triaxial Structures, in conjunction with MTL, Inc., Jessup, PA acquired the 3 domestic machines. Since that time TSI has been working to bring alive the remaining 3 domestic TWMs and is currently operating the first of these.
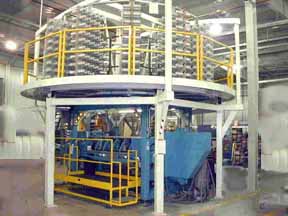
To examine in-depth the triaxial fabric technology please see our Tech Papers page.